A Note on CRCP Life-cycle Analysis
Best Practices and Assumptions
by Michael N. Plei, PE
Motivation
Many state transportation departments (DOTs) use life-cycle cost analysis (LCCA), or an equivalent approach, to decide which pavement is appropriate in building a new road project or in rehabilitating an old one.
One pavement option available to DOTs is continuously reinforced concrete pavement (CRCP). This road technology has been around for nearly 100 years. However, a modern approach to CRCP design and construction — based on best practices — has been used for the last 30 years.
This Technical Note provides guidance on using LCCA as it applies to today’s CRCP.
Assumptions
The modern design of CRCP includes sufficient:
- Concrete slab thickness to carry expected truck volumes and loads.
- Structure support for the base, subbase and treated subgrade to handle the expected traffic loads, and be non-erodible due to moisture and loads.
- Concrete strength and reinforcing steel content.
- Edge support, either provided by a tied concrete shoulder or by a widened slab, to move truck loads away from an unsupported pavement edge.
Typical Life-cycle Components
A typical life-cycle cost analysis of road pavements includes the following major considerations:
- Routine Maintenance
- Major Repairs
- Surface Restoration
- Salvage Value
These elements will be explored in the following sections.
Routine Maintenance
The relatively routine maintenance required for CRCP is resealing of the joints, which is similar to that required for the LCCA of jointed plain concrete pavement (JPCP).
In CRCP this resealing is limited to the longitudinal joints in between the mainline lanes, and in between the mainline lanes and the shoulders. Especially important is the joint between a concrete slab and asphalt, since there is nothing tying them together and thus tend to separate.
Common practice (based on published LCCA guidelines by state DOTs) is to reseal joints every 20 years, while the concrete surface is bare.
Transverse control joints in CRCP are limited to the pavement ends. These joints can be disregarded in a LCCA, since their length is short in comparison to a lane-mile of pavement. Typically pavement ends do not occur very often unless the highway is in an urban area with many structures.
Major Repairs
Repairing concrete highway pavements usual requires patching deteriorated sections and sometimes the supporting layers. For CRCP a major repair would involve patching a failed area called a punchout. The conclusion offed in this Technical Note is that, based on evidence compiled over the past 30 years, major repairs of CRCP are so infrequent that they can be eliminated from the LCCA.
CRCP built over the last 30 years have performed remarkably well. In fact, the historical failure mechanism of CRCP — punchouts — has largely been eliminated through use of proper concrete slab thickness, adequate longitudinal steel content, non-erodable bases, and tied shoulders.
Two references verify this - AASHTO M-E pavement software and state agency research, specifically from Texas. Using the AASHTO M-E, a pavement engineer would design the CRCP to have fewer that 10 punch puts per mile. While TxDOT’s studies of its CRCP inventory shows 1 punchout occurring for every 8.8 miles of CRCP. Other CRCP user states, such as Illinois, Oklahoma, Oregon, Georgia, California, Virginia, etc., can also corroborate this effect through researched and anecdotal evidence.
In other words, a well-designed and well-constructed CRCP will not require so few concrete patches (at most less than 10 per mile) through its 20-30 year design life. Therefore, the Major Repairs category of the LCCA can be ignored.
For more information on this topic please see the Appendix section which provides case study information to support this conclusion.
Surface Restoration
State transportation agencies have various methods to address rehabilitation of the concrete surface of CRCP. Today, that is typically required at 25 years (or, in some cases 30 years). At this time, the surface may need rehabilitation to restore friction (retexture) and/or ride quality (smoothness). This is done primarily in one of two ways: either the concrete surface is restored through a retexturing method (such as diamond grinding) or by applying a thin asphalt overlay (typically 2 - 4 inches).
Depending on the length of the LCCA, surface restoration may only need to be done once, or can be scheduled to be done at repeating intervals. Both activities can last 10 years, and in many cases, the asphalt life can exceed 15 years. Ideally, the first restoration would be to retexture and the second, if it fits into the LCCA period, would be to apply an asphalt overlay.
The major factor for longevity of an asphalt overlay on top of CRCP is that there is no reflective cracking through the asphalt layer. (As would typically appear in jointed plain concrete pavement (JPCP).) In CRCP, pavement cracks remain tight, and the insulating and waterproofing effects of the asphalt extends the CRCP service life. It should be noted that the asphalt overlay discussed here provides no structural strength to the pavement.
While suitable as a surface restoration method, bonded concrete overlays are more typically used to add structural strength to the existing pavement. This may be warranted where actual traffic levels or wheel loadings exceed the estimated levels used for the initial pavement design.
Salvage Value
The inclusion of any monies in an LCCA from the value of a CRCP at the end of the analysis period is up to the DOTs, but with complete removal of the CRCP, the constituent broken concrete and the steel reinforcing bars can easily be recycled; the steel being sold for scrap. The steel reinforcing bars are used to produce new products and the concrete can be crushed and reused as an aggregate base or as aggregate for new concrete pavement.
Recommendations
Activities and timing are discussed in greater detail in the previous sections are shown in the following table. The table provides a general guidelines overview on the type and timing of key events for CRCP in the Life-Cycle Cost Analysis.
Activity | Year |
---|---|
Initial Construction | 0 |
Routine Maintenance – Joint Sealing | 20 |
Surface Restoration – Retexturing | 25 |
Surface Restoration – Retexturing or AC Overlay | 35 |
Surface Restoration – AC Mill & Overlay | 45+ |
Salvage | EOL |
Table. 1 CRCP - Typical Timing of Key Events. Note: These activities and timing should be based on measured performance where available.
Appendix - Case Studies on Punch-outs
AASHTO M-E Pavement Analysis
To take a conservative approach, consider using the current AASTHO M-E software[1]. It has the ability to model a given pavement structure’s performance during the selected design life. For CRCP that performance is defined by ride roughness (IRI) and number of failures (punchouts).
AASHTO M-E software analysis include failure outputs — punchout (PO) — which shows the development of POs during the design life for a given pavement structure and site environment and truck loadings.
According to the software documentation, a highway pavement design for CRCP is considered to be acceptable if less than 10 POs develop over the design life, given a certain level of reliability. For highways that level of reliability is 95%.
Keep in mind that that software was developed using CRCP performance data and projects from as far back as the 1960s. Modern designed CRCP rarely develop punchouts, since the failure mechanisms are well understood and its causes avoided.
According to the Guide for Mechanistic-Empirical Design of New and Rehabilitated Pavement Structures the following distress types and severity levels are recommended for assessing CRCP[2]:
Highway Class | Acceptable | Inadequate |
---|---|---|
Interstate/ Freeway |
≤ 10 | > 10 |
Primary | ≤ 15 | > 15 |
Secondary | ≤ 20 | > 20 |
Table. 2 Load Related Distress Level: CRCP Punch-outs (medium- and high-severity) No. / lane-mile
Punch-outs per lane-mile | Percentage of lane-mile patched |
---|---|
0.125 | 0.014 |
0.2 | 0.226 |
1 | 0.113 |
4.4 | 0.5 |
8 | 0.9 |
9 | 1 |
10 | 1.1 |
22 | 2.5 |
44 | 5.0 |
Table. 3 Percentage of lane-mile patched based on the number of punch-outs repaired.
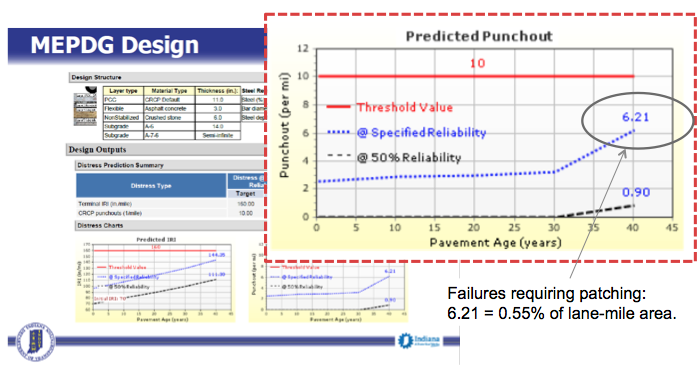
Fig. 1 Example from Indiana DOT I-65 South Split CRCP Design [Need Reference]
TxDOT Studies
TxDOT has recently studied the performance of its CRCP inventory with the following results.[3]
- Punch-out: 1 per 8.8 lane-miles
- Concrete Patch: 1 per 4.6 lane-miles
- Asphalt Patch: 1 per 88 lane-miles
The rate of increase (for the entire state CRCP inventory) is about 0.05 distresses per lane-mile per year.
Also note that an asphalt patch is placed as a temporary solution, and will need to be replaced with a concrete patch at some point.
Conclusion [ Need some words here]
TxDOT PMIS Annual Report[4]
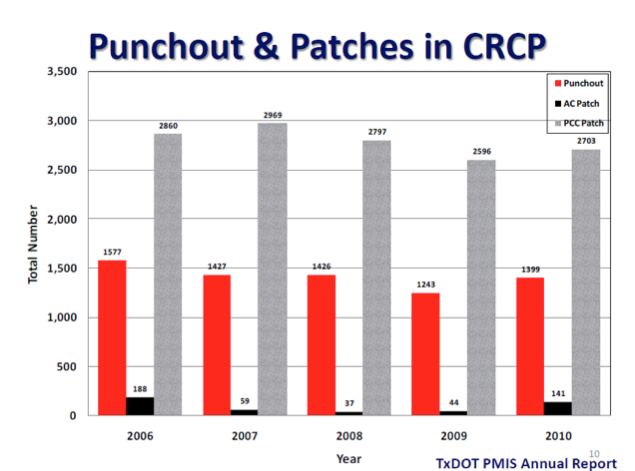
Fig. 2 TxDOT PMIS Annual Report [Need Reference]
Conclusion: Historical CRCP failure mechanisms have been eliminated with modern designs [ Need some words here]
TxDOT CRCP Patching, based on quantities from “AVERAGE LOW BID UNIT PRICES” [Need Reference]
Year, Range | Equiv. Lane-miles | Avg. Cost per SY |
---|---|---|
Unknown | 7.9 | $158 |
5/2008-5/2009, Const. | 6.1 | $128 |
5/2008-5/2009, Maint. | 4.3 | 186 |
5/2010-5/2011, Const. | 4.5 | $147 |
5/2010-5/2011, Maint. | 7.9 | $182 |
12/2013-12/2014, Const. | 5.9 | $153 |
12/2013-12/2014, Maint. | - | - |
1/2015-1/2016, Const. | 4.6 | $190 |
1/2015-1/2016, Maint. | 1.3 | $316 |
Table. 4 TxDOT CRCP Patching, based on quantities from “AVERAGE LOW BID UNIT PRICES”.
Belgium Case Study[5]
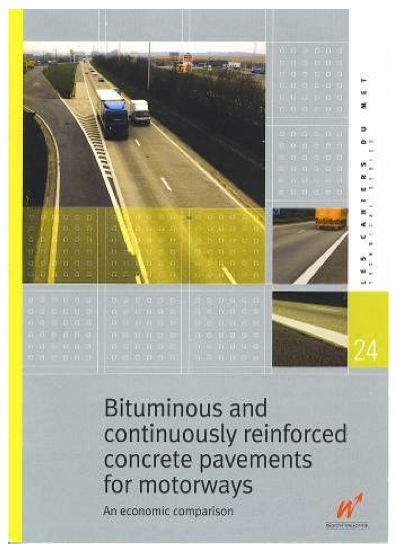
Fig. 3 Bituminous and Continuously Reinforced Concrete Pavements for Motorways Report [Need Reference]
In-depth life-cycle cost study performed by the Belgium Ministry, that includes both asphalt and CRCP. The Ministry used actual cost and performance data from their road inventory to compare the alternatives
Section 6.2.2 Localized Repairs in Continuously Reinforced Concrete (p. 30) The report contains information on the expected frequency of repair as summarized in the following table.
Shoulder Type | No. of POs |
---|---|
Asphalt | 1 every 3 years |
Concrete, Tied | 1 every 10 years |
Table. 5 Expected Frequency of Localized Repairs in Continuously Reinforced Concrete (CRCP).
References
- ^ Continuously Reinforced Concrete Pavement: Design Using the AASHTO Ware Pavement ME Design Procedure, PUBLICATION NO. FHWA-HIF-13-025, April 2013
- ^ Guide for Mechanistic-Empirical Design of New and Rehabilitated Pavement Structures, NCHRP 1-37a, Table 2.5.15. Distress types and severity levels recommended for assessing rigid pavement structural adequacy (at the time of evaluation)., Pg 63
- ^ TECHNICAL MEMORANDUM – MTIA018-2(b), Moon Won, Center for Multidisciplinary Research in Transportation, Texas Tech University, to Lisa Lukefahr, Texas Department of Transportation, July 31, 2011
- ^ TRB CRCP Webinar-Design, 2011 by Moon Won, Texas Tech University.
- ^ Bituminous and Continuously Reinforced Concrete Pavements for Motorways – An Economic Comparison by the General Directorate of Motorways and Roads, Walloon Ministry of Infrastructure and Transport, Belgium, September 2008